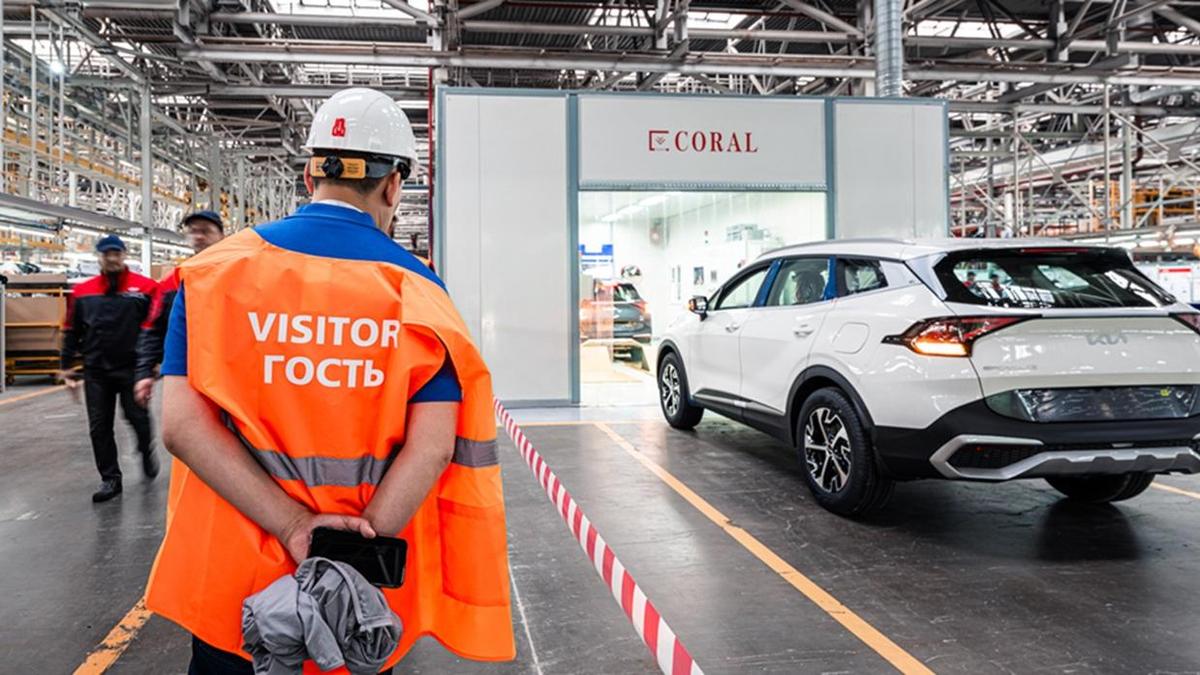
В Казахстане обсуждается петиция по вопросам утилизационного сбора, авторы которой критикуют отечественных машиностроителей. Однако, показатели автомобилестроения ежегодно улучшаются: по итогам 2023 года в стране выпущено почти 150 тысяч легковых автомобилей. По данным Казахстанского автомобильного союза, доля автопрома в машиностроении Казахстана составляет 43%. О том, как работает крупнейший автомобильный завод страны – в фоторепортаже из Костаная.
Автомобильный завод Allur расположен в индустриальной зоне Костаная. Из центра города до завода можно добраться за минут 10. Сейчас на костанайском заводе выпускают четыре модели легковых автомобилей полного цикла: Kia Cerato, Kia Sportage, Chevrolet Onix и JAC S3.
Костанайское автомобилестроительное предприятие занимает 350 тыс. кв.м, из них 86 тыс. кв.м – производственные площади. История нового автомобиля начинается с этой локации с названием "Склад деталей".
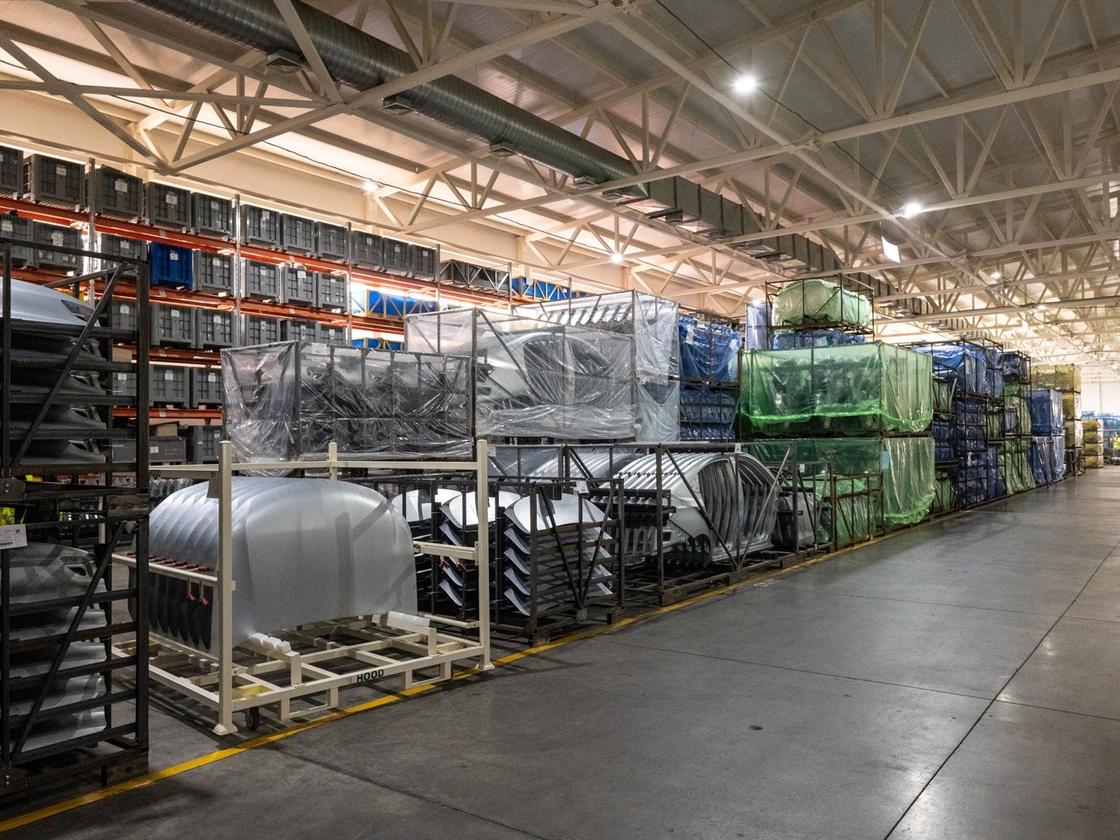
Виталий Христ, операционный директор Allur, отметил:
"Сюда поступают автомобильные детали от наших заводов-партнеров, которые далее направляются на участки комплектовки. Под компоненты отведены два помещения, которые позволяют нам хранить порядка 500 машинокомплектов. Это общее количество деталей, которые у нас находятся в изготовлении кузова автомобиля".
Информация по автомобильным компонентам заносится в специальную информационную базу данных. Электронная картотека ВМС - отображает полную информацию по каждой автомобильной детали на складе. Цифровизация упростила часть сложных процессов на автозаводе.
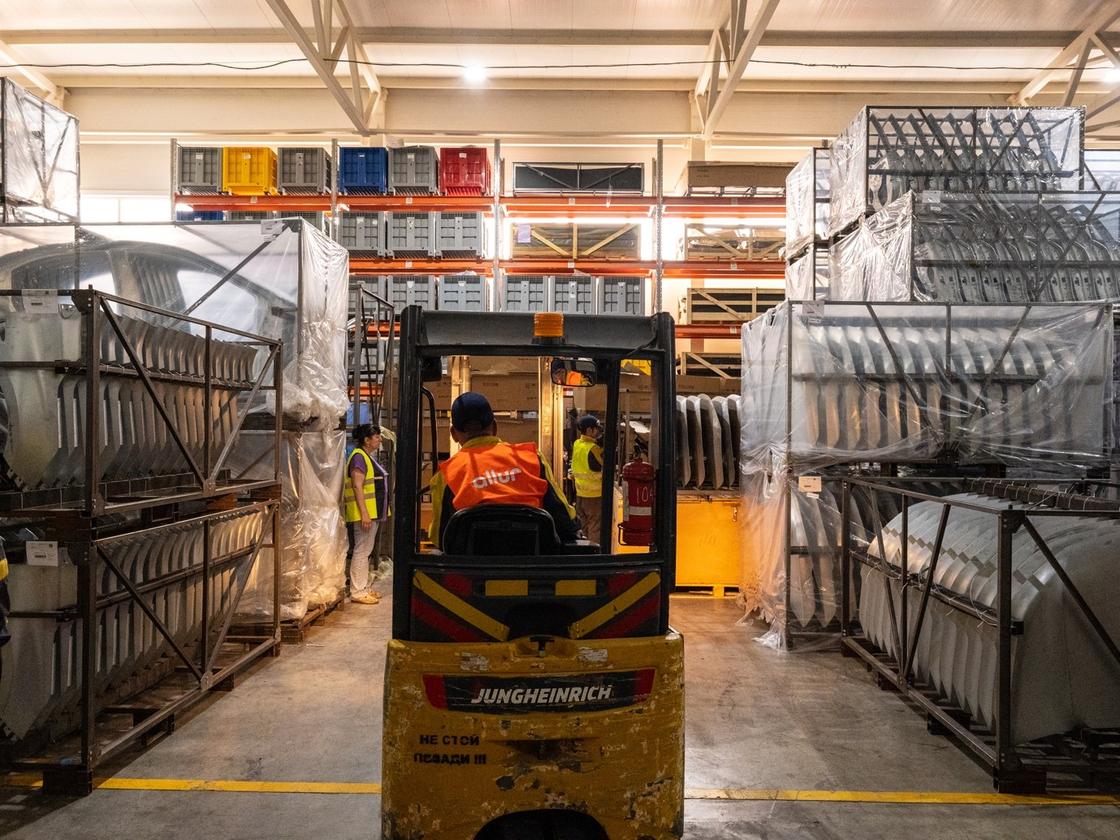
Отобранные автокомпоненты направляются на участок комплектовки и далее в сварочные цеха автомобиля. Сварочных линий на заводе Allur четыре, отдельная для каждой выпускаемой модели авто.
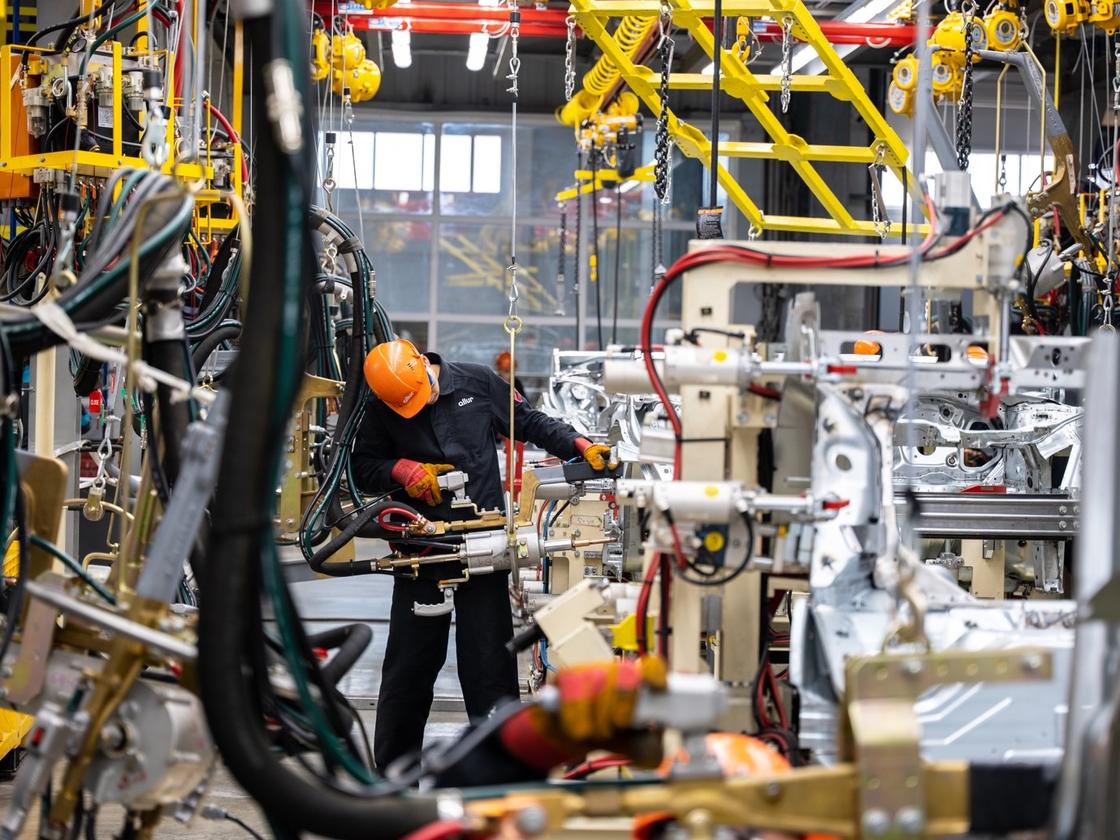
Для производства Chevrolet Onix на заводе используют роботизированную лазерную сварку.
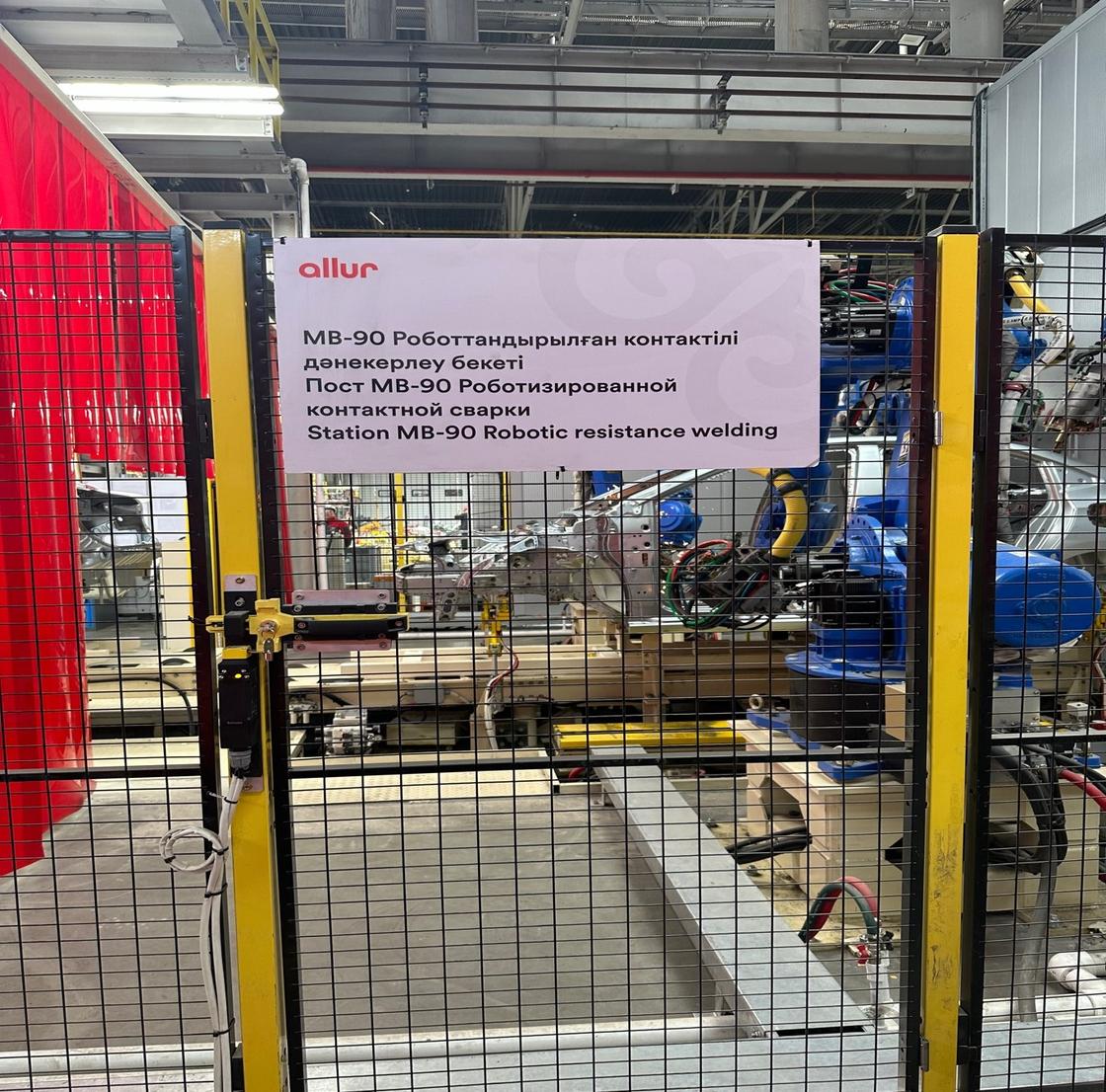
"Автоматизация позволила повысить производительность, гарантируя необходимый уровень сварки. Данная линия оснащена двумя необходимыми постами. Одна из них является уникальной с точки зрения современной технологии приварки крыши кузова, она выполняется лазерной сваркой. Она позволяет избегать присутствия дополнительных операций в зоне смыкания крыши с боковиной, при этом обеспечивая необходимый уровень прочности и качества геометрии", - рассказал Виталий Христ, операционный директор Allur.
Финальные штрихи сварочного цеха – геометрия кузова. Каждая деталь у опытных инженеров как под микроскопом. Допуск на следующий уровень получают только проверенный и соответствующий конструкторской задумке металлический корпус авто.
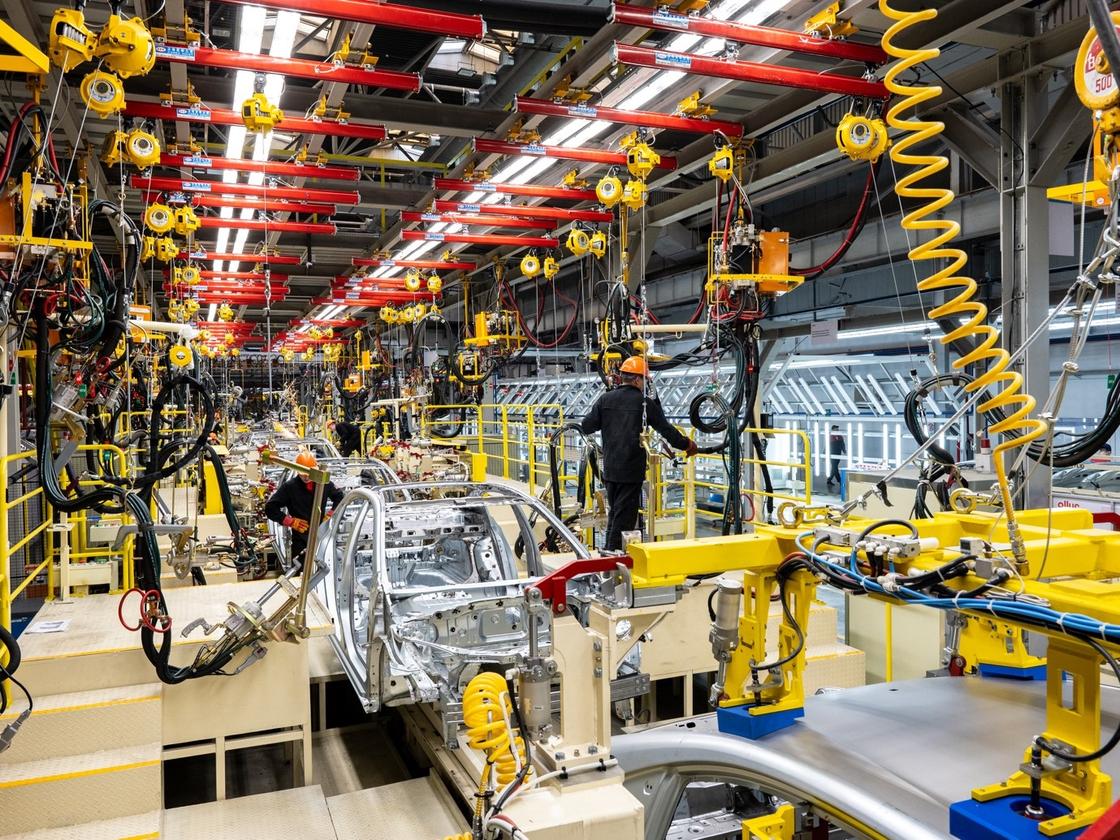
"На каждой из сварочных линий у нас 300-400 сварочных соединений, важно соблюдать последовательность, необходимое количество соединений. Финальная часть кузова, которая является несущей конструкцией, куда крепятся узлы и элементы интерьера автостекла и так далее, нам крайне важно, чтобы эта часть работала с точки зрения техрегламента и безопасности, как задумано конструкторами данного авто. Выполнение данной моделью всех характеристик важно так как это влияет на безопасную эксплуатацию конкретного авто потребителем", - добавил Виталий Христ.
Будущую автопродукцию испытывают на всех этапах производства. Сдача тестов на прочность, надежность и безопасность проходит в лабораторных условиях.
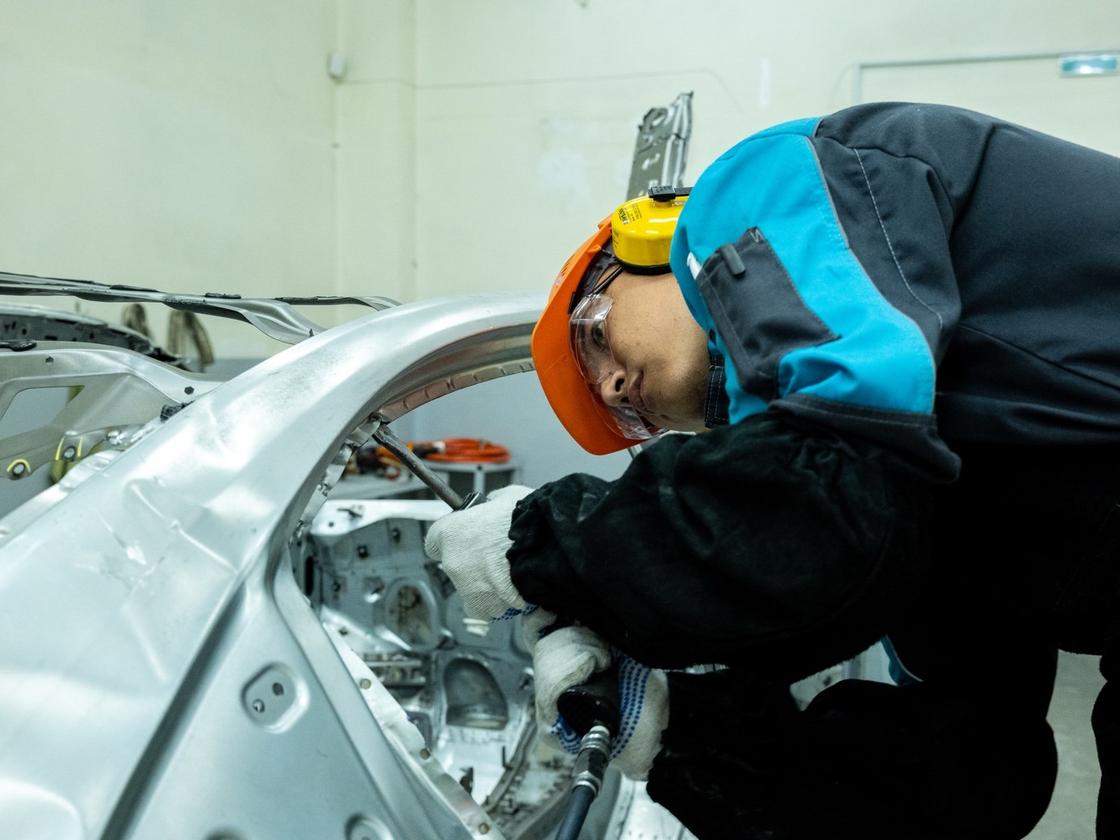
Все помещения оснащены современным оборудованием, точь как на ведущих заводах-партнерах.
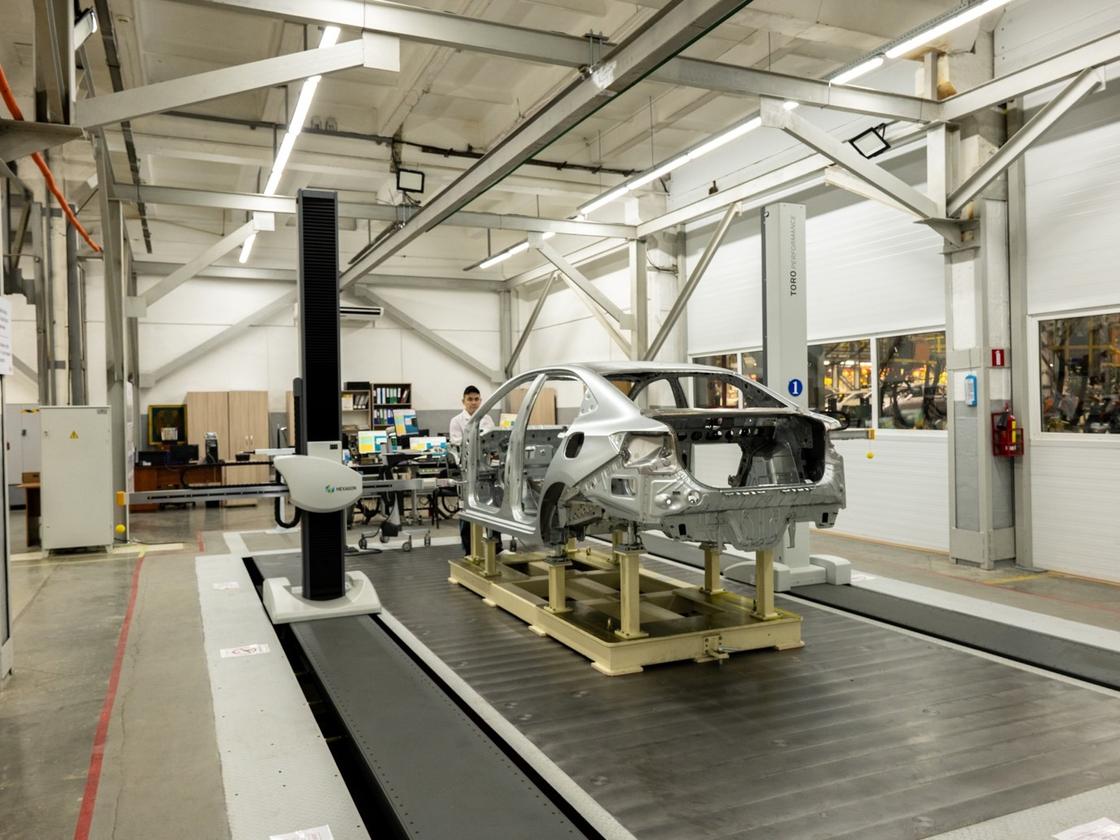
Далее следуем в цех покраски кузова. Процесс состоит из нескольких этапов: сначала кузов обрабатывают антикоррозийным покрытием, грунтуют, окунают в катафорезную краску, наносится мастика далее кузов проходит вторичный грунт, лакокрасочную линию и финальную покраску.
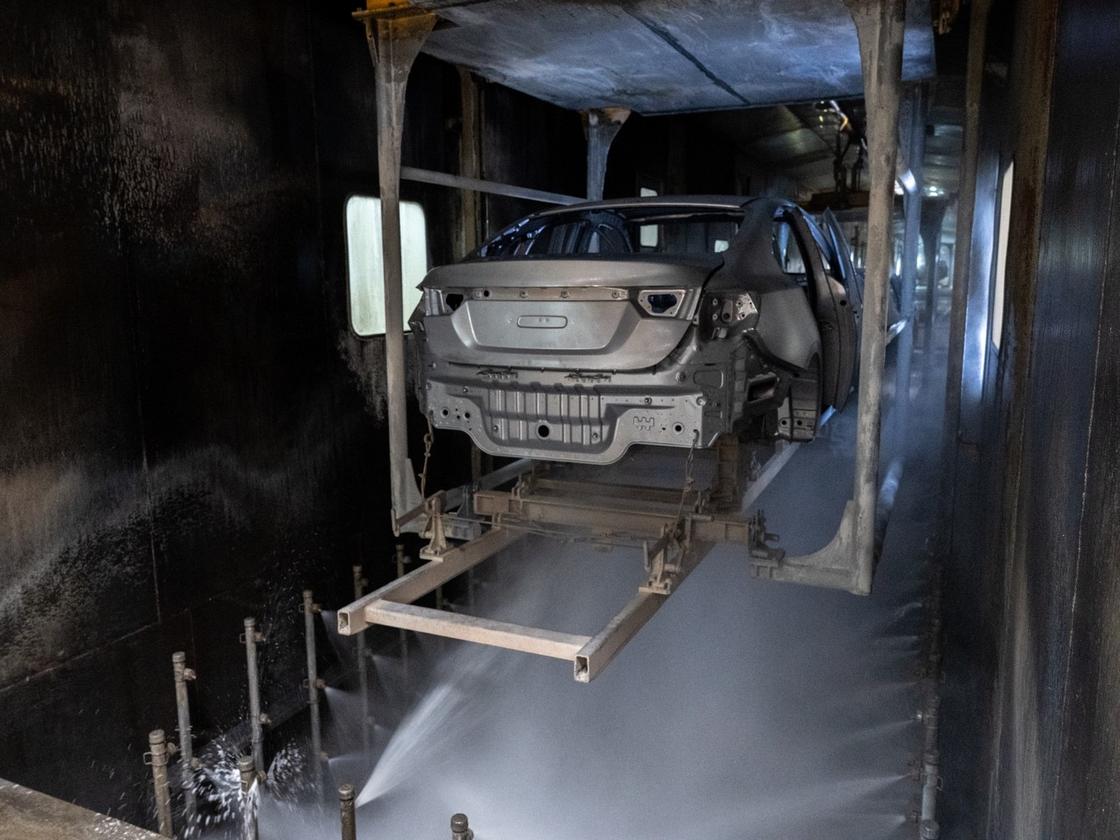
Все процессы чередуются и детали проходят через печь для обеспечения твердости покрытия. Сейчас на заводе используют пять оттенков для окрашивания авто. Все материалы для покраски одобрены заводами-партнерами.
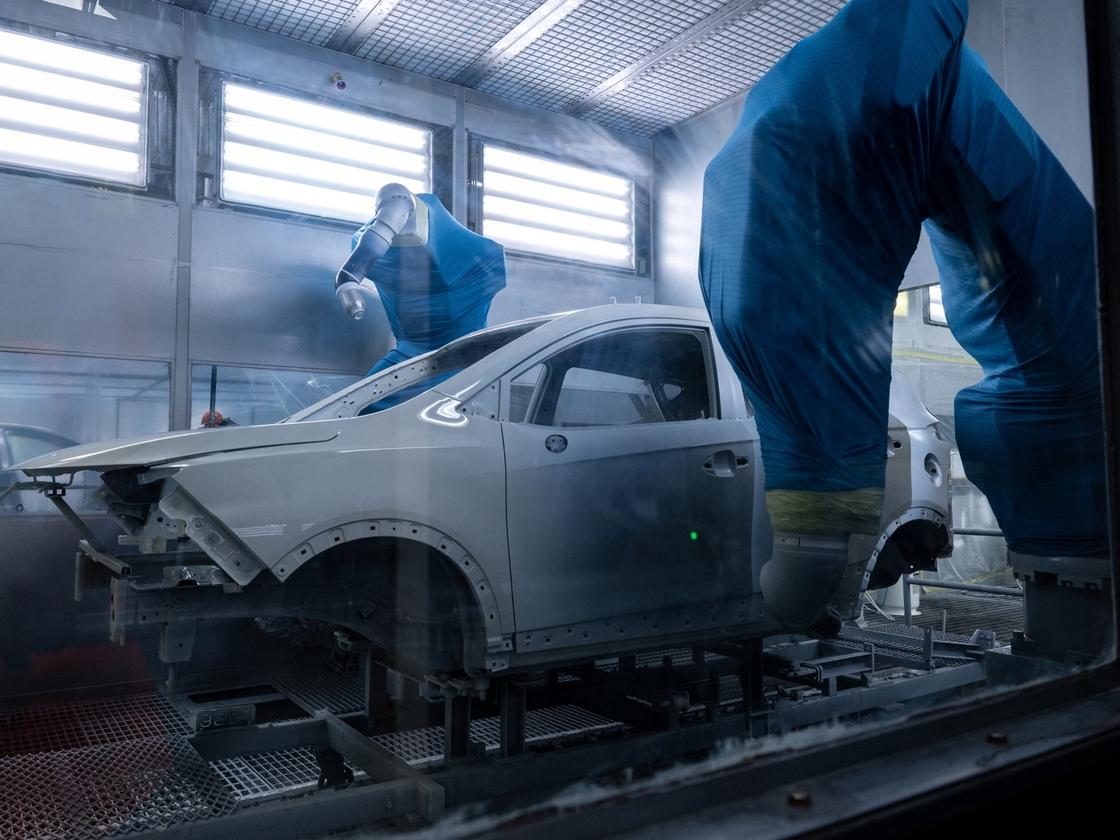
Сейчас на заводе завершают пуско-наладочные работы цеха по окраске пластиковых деталей автомобиля.
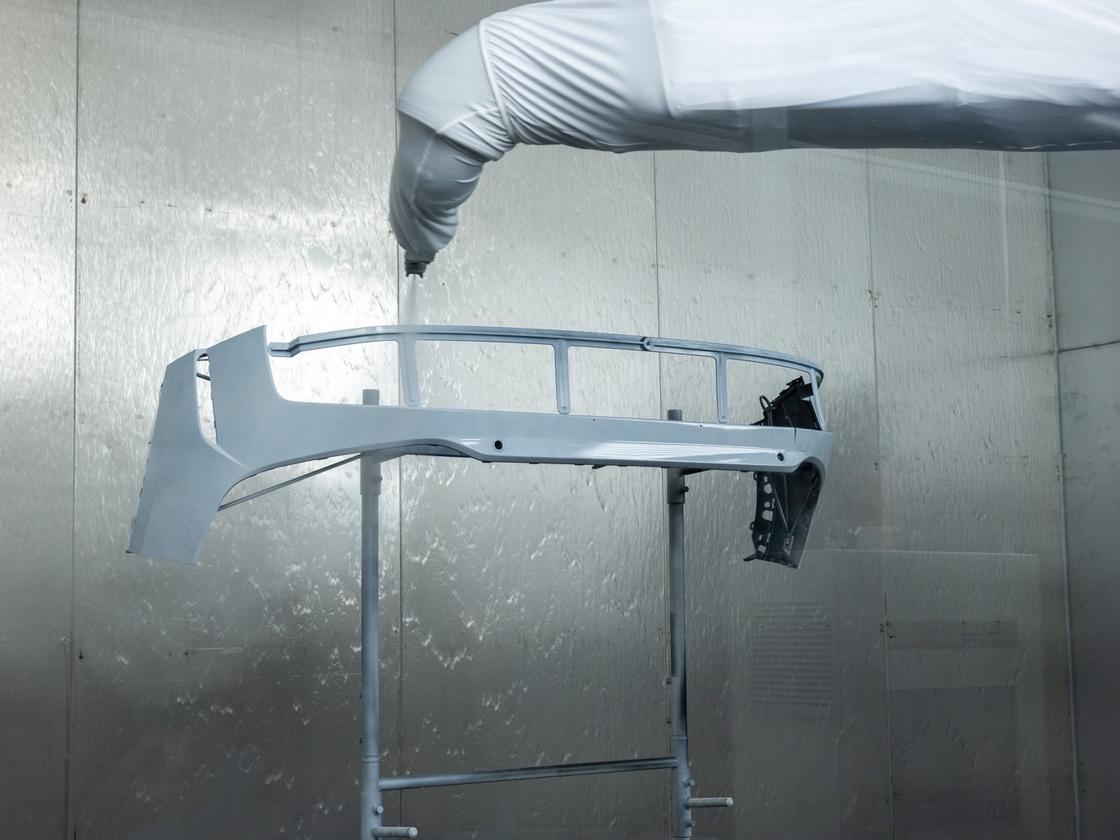
"Это новый для нас производственный цех с высокой степенью автоматизации. Шесть роботов, которые позволяют окрашивать до 6 тыс. комплектов пластиковых деталей авто в год. Запуск данного цеха позволит разгрузить мощности, которые мы сейчас используем для покраски авто и увеличить количество выпускаемых кузовов", - поделился Виталий Христ, операционный директор Allur.
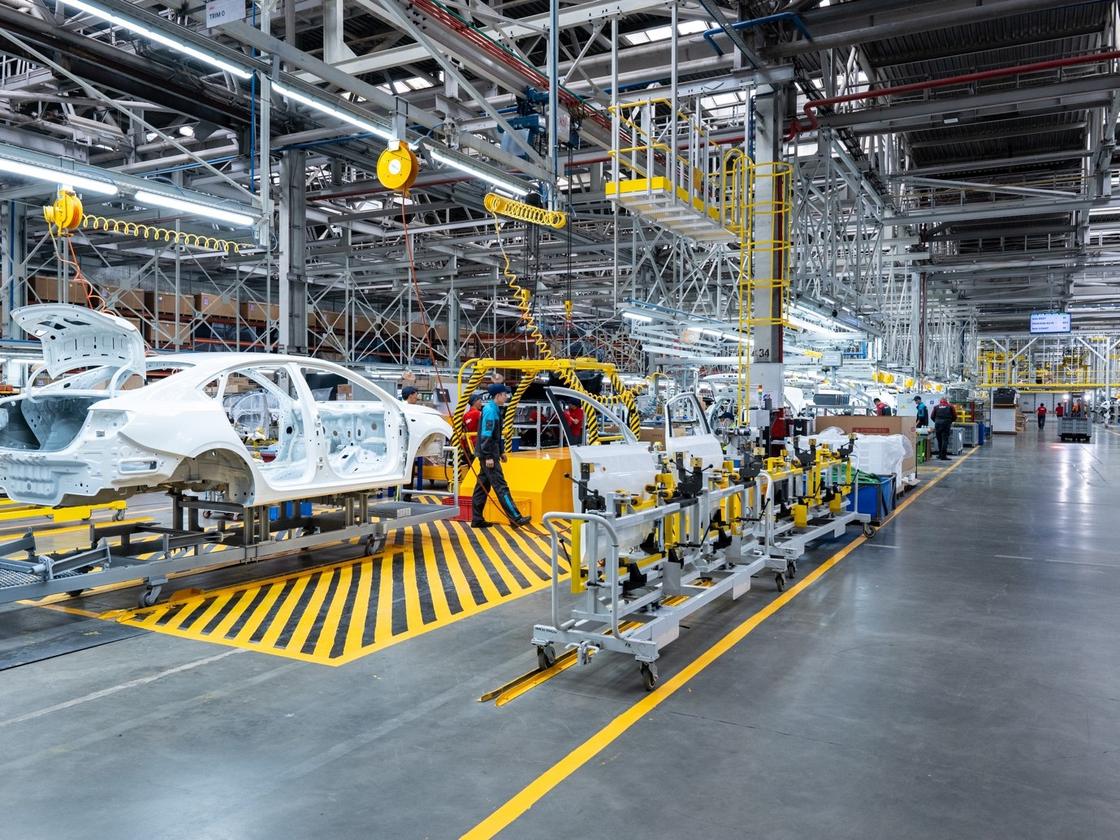
Следующий этап сборка автомобиля. Процесс состоит из трех этапов: на первой линии собирается салон, далее идет сборка шасси автомобиля и под занавес процессов – собирается интерьер, осуществляется программирование ТС и заправка техжидкостями.
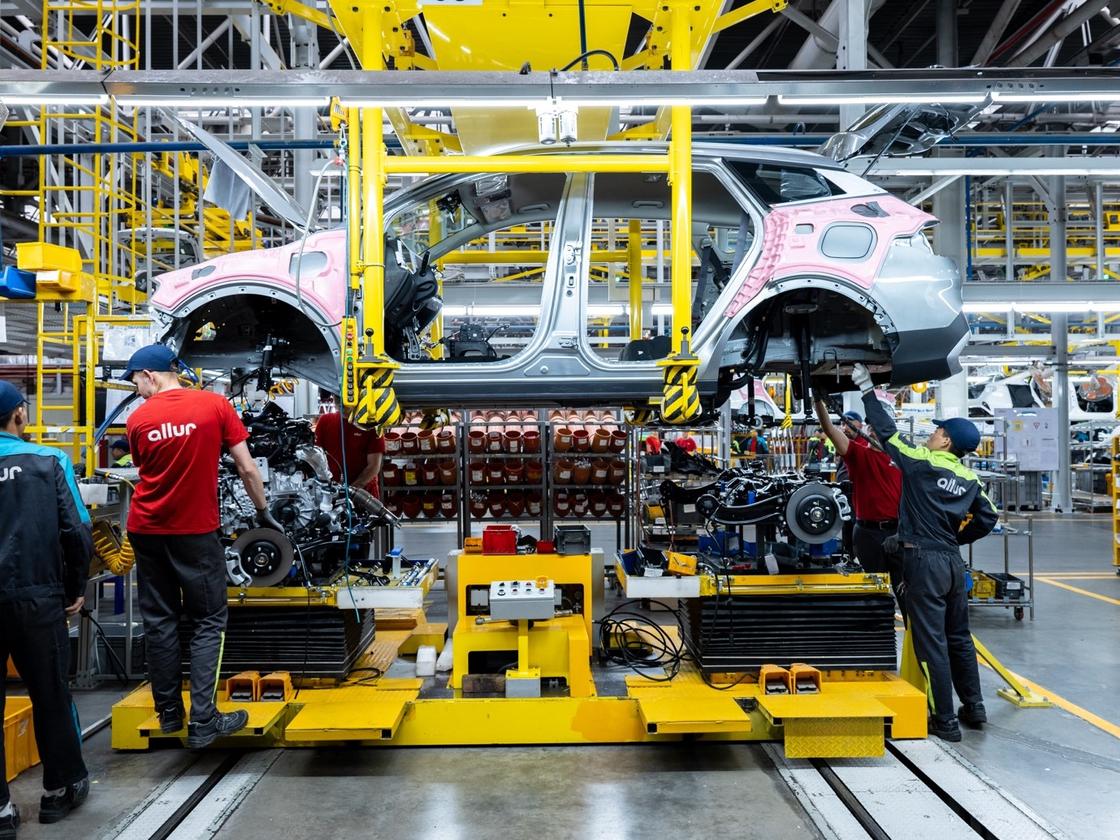
На заводе два цеха по сборке автомобилей. Один из них - мелкоузловая сборка, она была запущена в начале 2023 года. Уникальность технологии состоит в сборке авто разных моделей, что оптимизировало часть сложных процессов. Производительность линии - 8 авто в смену.
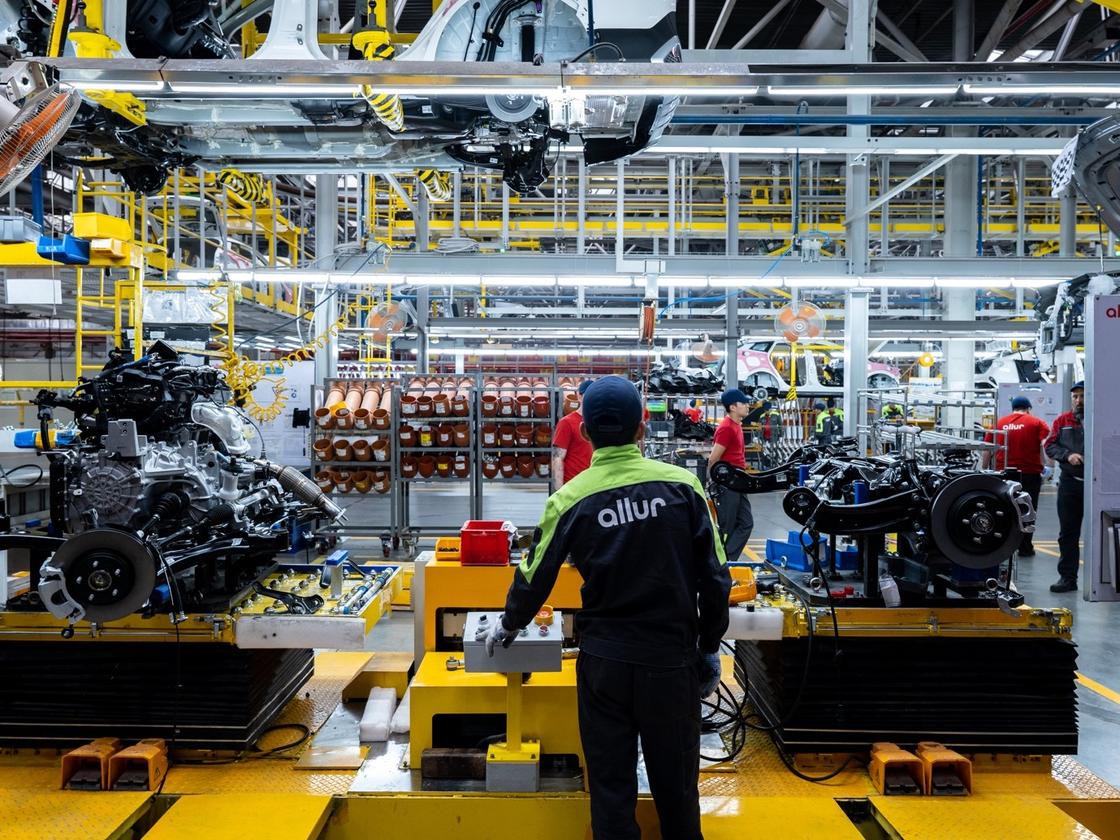
"Здесь монтируются, в первую очередь, электроповода, шумоизоляция, устанавливаются стекла авто, панель приборов и остальные элементы авто. Здесь собираются три модели различных конфигураций. Количество сборочных операций на одну модель от 800 до 1 400 операций в зависимости от конфигурации кузова", - добавил специалист.
До выхода в серийное производство, автомобиль проходит еще несколько высокоточных испытаний. На заводе Allur имеется специальная тестовая линия, которая имитирует дорожное покрытие и даже аварийные ситуации.
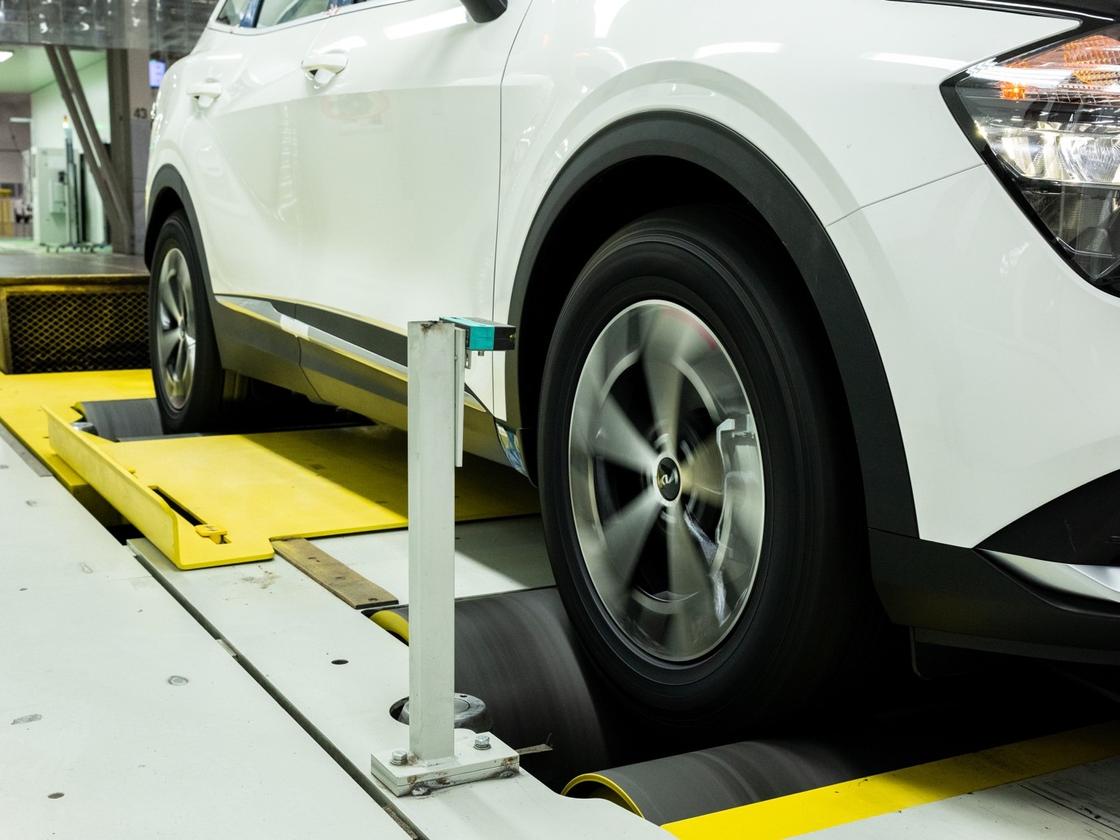
Положительное заключение – "зеленый свет" конвейерному производству модели. На заводе планируют в этом году выпустить порядка 17 тыс. авто полного цикла по смешанному типу производства.
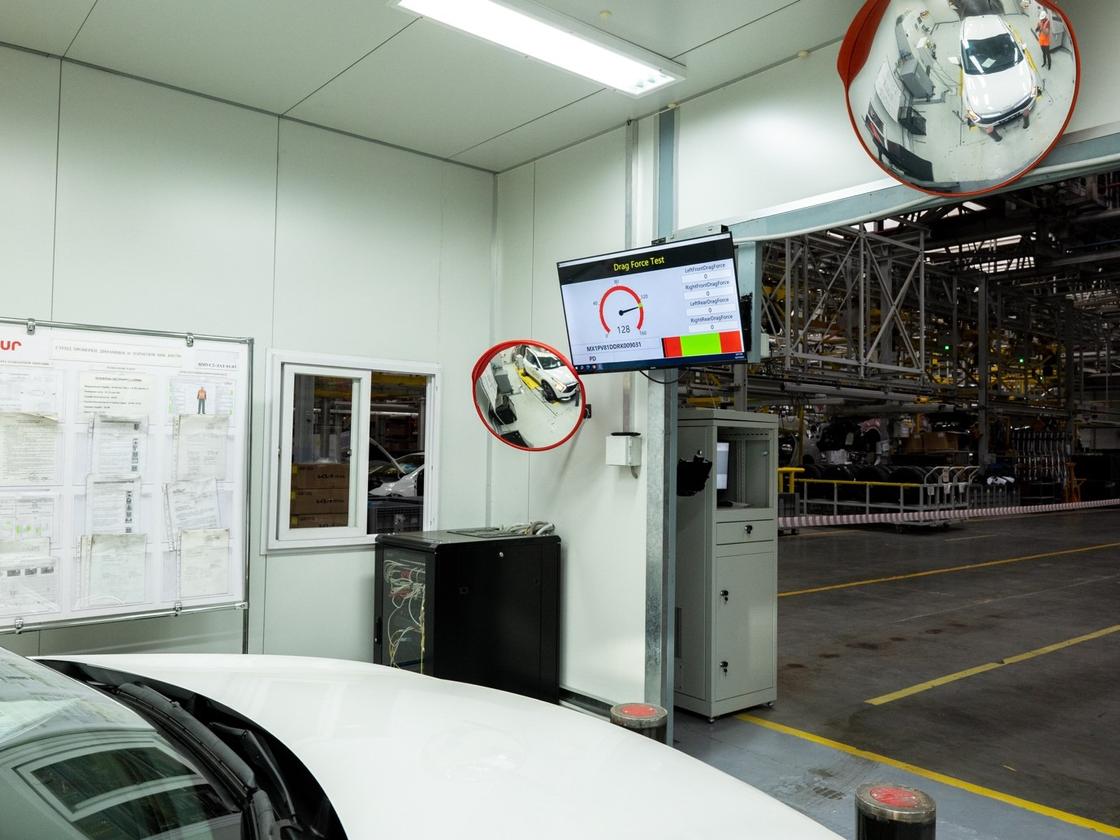
Большое внимание на автомобильном заводе уделяют подготовке и повышению квалификации своих кадров. На предприятии функционирует корпоративный университет Allur.
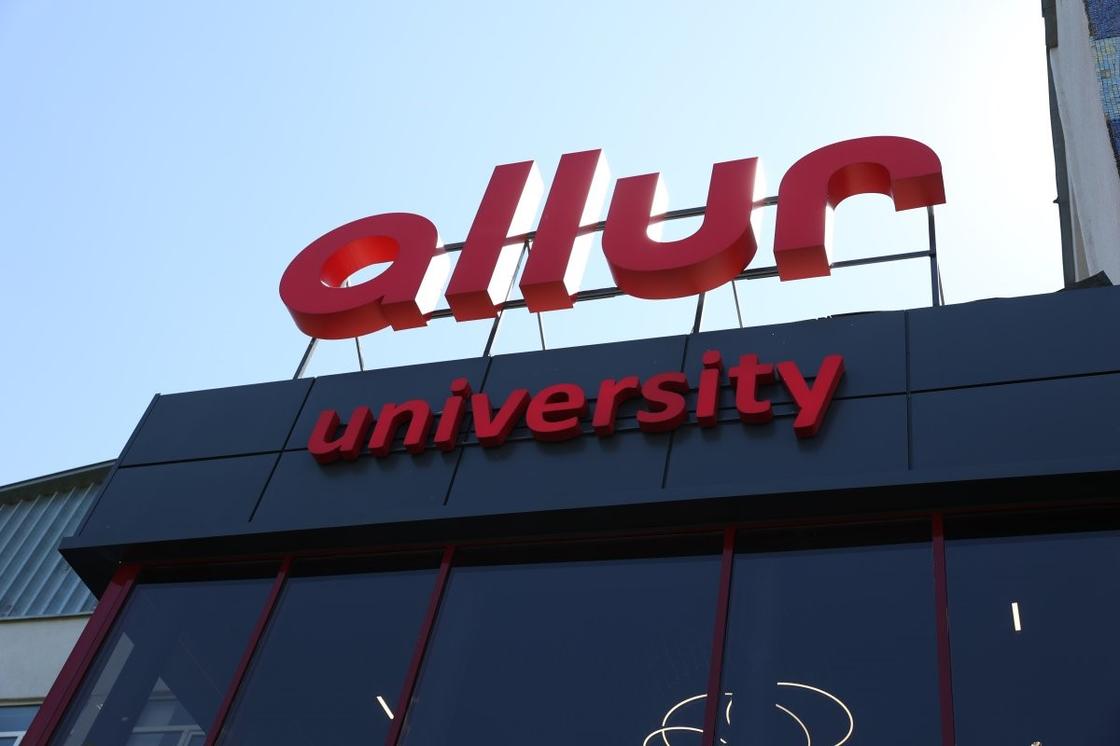
Касательно планов по локализации, то они уже обрели четкие очертания. Автозавод уже подписал контракты на закуп автомобильных шин, произведенных в городе Сарань. В работе заказы автомобильных сидений, дисков, систем автомобильного выхлопа. По темпам производства, также планируется нарастить объемы производства автомобилей до 120 тыс. единиц транспортных средств в год и запустить несколько льготных автопрограмм. А это значит, что автомобилей казахстанского производства на дорогах будет еще больше.